AI Predictive Maintenance: Cutting Downtime by 15% in US Manufacturing by 2025
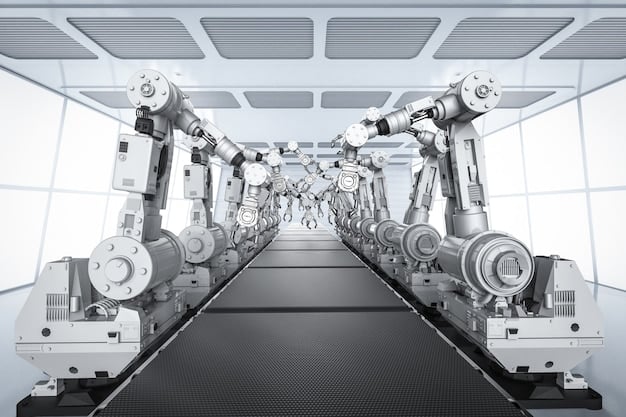
AI-powered predictive maintenance is poised to revolutionize US manufacturing by 2025, offering the potential to slash equipment downtime by 15% through advanced data analysis and proactive maintenance strategies, leading to increased efficiency and reduced operational costs.
Imagine a future where factory floors hum with uninterrupted productivity, all thanks to the power of data. That future is closer than you think, as AI-powered predictive maintenance promises to cut equipment downtime by 15% in US manufacturing by 2025.
The Rise of Predictive Maintenance in Manufacturing
Predictive maintenance is no longer a futuristic concept; it’s a present-day solution that’s rapidly transforming the manufacturing landscape. By leveraging advanced technologies like artificial intelligence, manufacturers can move away from reactive and preventive maintenance strategies to a more proactive and efficient approach.
This shift is driven by the increasing availability of sensor data, powerful computing resources, and sophisticated AI algorithms that can analyze complex patterns and predict potential equipment failures before they happen. The result is reduced downtime, lower maintenance costs, and increased overall productivity.
What is Predictive Maintenance?
At its core, predictive maintenance involves using data analysis techniques to monitor the condition of equipment and predict when maintenance will be required. This allows maintenance activities to be scheduled proactively, minimizing disruptions to production and preventing costly breakdowns.
Unlike traditional maintenance approaches, predictive maintenance is based on real-time data and ongoing analysis. This means that maintenance is only performed when it’s actually needed, rather than on a fixed schedule. This can lead to significant cost savings and improved equipment reliability.
Benefits of Predictive Maintenance
- Reduced Downtime: By predicting and preventing equipment failures, predictive maintenance can significantly reduce unplanned downtime, keeping production lines running smoothly.
- Lower Maintenance Costs: Predictive maintenance optimizes maintenance scheduling, reducing the need for unnecessary maintenance activities and minimizing the costs associated with emergency repairs.
- Improved Equipment Reliability: By identifying and addressing potential problems before they lead to breakdowns, predictive maintenance can extend the lifespan of equipment and improve its overall reliability.
- Increased Productivity: With less downtime and more reliable equipment, manufacturers can increase their overall productivity and meet customer demand more effectively.
In conclusion, predictive maintenance offers a powerful way for manufacturers to optimize their maintenance operations, reduce costs, and improve overall productivity. By leveraging the power of data and AI, manufacturers can unlock new levels of efficiency and competitiveness.
How AI Powers Predictive Maintenance
Artificial intelligence is the engine that drives modern predictive maintenance systems. AI algorithms can analyze vast amounts of data from sensors, historical records, and other sources to identify patterns and predict future equipment failures with remarkable accuracy.
AI’s ability to learn and adapt makes it particularly well-suited for predictive maintenance applications. As more data becomes available, AI algorithms can refine their predictions and improve their accuracy over time. This leads to more effective maintenance decisions and better overall results.
Key AI Technologies Used in Predictive Maintenance
Several AI technologies play a crucial role in enabling predictive maintenance. These include machine learning, deep learning, and natural language processing. Each of these technologies offers unique capabilities that contribute to the overall effectiveness of predictive maintenance systems.
Machine learning algorithms can be trained to identify patterns in data that are indicative of potential equipment failures. Deep learning models can analyze more complex data sets, such as images and videos, to detect subtle signs of wear and tear. Natural language processing can extract valuable insights from maintenance logs and other textual data.
The Role of Data in AI-Powered Predictive Maintenance
Data is the lifeblood of AI-powered predictive maintenance systems. The more data that is available, the more accurate and reliable the AI’s predictions will be. This data can come from a variety of sources, including sensors, historical maintenance records, and equipment manuals.
Sensor data is particularly valuable because it provides real-time insights into the condition of equipment. By monitoring parameters such as temperature, vibration, and pressure, sensors can detect subtle changes that may indicate an impending failure. This data is then fed into AI algorithms, which analyze it to predict when maintenance will be required.
In summary, AI is the key enabler of predictive maintenance, allowing manufacturers to harness the power of data to predict equipment failures and optimize maintenance schedules. By leveraging AI technologies, manufacturers can achieve significant cost savings, reduce downtime, and improve overall productivity.
US Manufacturing: A Prime Candidate for AI Predictive Maintenance
The US manufacturing sector stands to benefit significantly from the adoption of AI-powered predictive maintenance. With its aging infrastructure and increasing global competition, US manufacturers need to find new ways to optimize their operations and improve their competitiveness.
Predictive maintenance offers a powerful solution to many of the challenges facing US manufacturers. By reducing downtime, lowering maintenance costs, and improving equipment reliability, predictive maintenance can help US manufacturers become more efficient, competitive, and resilient.
Challenges and Opportunities in US Manufacturing
The US manufacturing sector faces a number of challenges, including an aging workforce, increasing energy costs, and growing regulatory burdens. However, these challenges also present opportunities for innovation and improvement. By embracing new technologies like AI and predictive maintenance, US manufacturers can overcome these challenges and thrive in the global marketplace.
One of the biggest challenges facing US manufacturers is the skills gap. As experienced workers retire, there is a shortage of skilled workers to replace them. This makes it even more important for manufacturers to adopt technologies that can automate tasks and improve efficiency.
- Aging Infrastructure: Many US manufacturing facilities have aging infrastructure that is prone to breakdowns and requires frequent maintenance. Predictive maintenance can help manufacturers extend the lifespan of their equipment and avoid costly replacements.
- Global Competition: US manufacturers face intense competition from companies in other countries that have lower labor costs and more modern facilities. Predictive maintenance can help US manufacturers level the playing field by reducing costs and improving efficiency.
- Regulatory Burdens: US manufacturers must comply with a complex web of regulations related to safety, environmental protection, and labor practices. Predictive maintenance can help manufacturers comply with these regulations by ensuring that equipment is properly maintained and operated safely.
In conclusion, US manufacturing is a prime candidate for AI-powered predictive maintenance. By embracing this technology, US manufacturers can overcome the challenges they face and seize the opportunities that lie ahead, ultimately leading to a more competitive and sustainable manufacturing sector.
The 15% Downtime Reduction Target: Realistic and Achievable
The goal of cutting equipment downtime by 15% in US manufacturing by 2025 through AI-powered predictive maintenance is ambitious but realistic. Several factors support this target, including the growing maturity of AI technologies, the increasing availability of data, and the proven track record of predictive maintenance in other industries.
Many early adopters of predictive maintenance have already achieved significant reductions in downtime and maintenance costs. As more manufacturers embrace this technology, the overall impact on the US manufacturing sector will be substantial.
Case Studies of Successful Predictive Maintenance Implementation
Numerous case studies demonstrate the effectiveness of predictive maintenance in reducing downtime and improving equipment reliability. These case studies span a variety of industries, including aerospace, automotive, and energy.
For example, a major aerospace manufacturer implemented a predictive maintenance system that reduced unplanned downtime by 20% and maintenance costs by 15%. An automotive company used predictive maintenance to identify and address potential problems on its assembly lines, resulting in a 10% increase in production output. A power generation company used predictive maintenance to monitor the condition of its turbines, preventing costly breakdowns and extending the lifespan of its equipment.
Factors Contributing to the 15% Reduction
Several factors are contributing to the growing adoption of predictive maintenance and the potential for significant downtime reductions. These include:
- Advancements in AI Technologies: AI algorithms are becoming more sophisticated and accurate, enabling more effective predictive maintenance.
- Increased Data Availability: The proliferation of sensors and other data sources is providing manufacturers with unprecedented insights into the condition of their equipment.
- Cloud Computing: Cloud computing platforms provide manufacturers with the computing resources they need to process and analyze large amounts of data.
- Falling Sensor Costs: The cost of sensors is decreasing, making it more affordable for manufacturers to deploy them throughout their facilities.
Therefore, the 15% downtime reduction target is not just a hopeful projection but is grounded in demonstrable success and supported by ongoing technological advancements and increasing accessibility of key enablers.
Implementing AI Predictive Maintenance: A Step-by-Step Guide
Implementing AI-powered predictive maintenance can seem daunting, but it doesn’t have to be. By following a structured approach and focusing on key areas, manufacturers can successfully deploy predictive maintenance systems and achieve significant improvements in their operations.
A successful implementation requires a clear understanding of the manufacturer’s goals, a commitment to data quality, and a willingness to embrace new technologies and processes.
Key Steps for Implementing Predictive Maintenance
The implementation process typically involves the following steps:
- Identify Critical Equipment: Start by identifying the equipment that is most critical to the manufacturing process and that is most prone to breakdowns.
- Gather Data: Collect data from sensors, historical maintenance records, and other sources.
- Choose an AI Platform: Select an AI platform that is specifically designed for predictive maintenance applications.
Overcoming Challenges and Ensuring Success
Manufacturers may face a number of challenges during the implementation process. These challenges can include:
- Data Quality Issues: Poor data quality can lead to inaccurate predictions and ineffective maintenance decisions.
- Lack of Expertise: Manufacturers may lack the expertise needed to deploy and maintain AI-powered predictive maintenance systems.
- Integration Challenges: Integrating predictive maintenance systems with existing IT infrastructure can be complex and challenging.
- Resistance to Change: Employees may resist the adoption of new technologies and processes.
Successfully implementing AI-powered predictive maintenance requires careful planning, a commitment to data quality, and a willingness to embrace new technologies and processes. By addressing these challenges head-on, manufacturers can unlock the full potential of predictive maintenance and achieve significant improvements in their operations.
The Future of Manufacturing: AI-Driven Efficiency and Reliability
The future of manufacturing is inextricably linked to the adoption of AI and predictive maintenance. As AI technologies continue to evolve and become more accessible, manufacturers will increasingly rely on them to optimize their operations, reduce costs, and improve their competitiveness.
In the years ahead, we can expect to see even more sophisticated AI-powered predictive maintenance systems that can analyze larger amounts of data, make more accurate predictions, and provide more personalized recommendations.
Emerging Trends in AI Predictive Maintenance
Several emerging trends are shaping the future of AI predictive maintenance. These include:
The integration of predictive maintenance with other manufacturing systems, such as enterprise resource planning (ERP) and manufacturing execution systems (MES). This integration will enable manufacturers to make more informed decisions about production planning, inventory management, and supply chain optimization.
The use of edge computing to process data closer to the source, reducing latency and enabling real-time decision-making. Edge computing is particularly useful for applications that require low latency, such as monitoring critical equipment in remote locations.
- The Rise of Digital Twins: Digital twins are virtual representations of physical assets that can be used to simulate their behavior and predict their performance.
- The Ubiquitous Deployment of IoT Sensors: The Internet of Things (IoT) is enabling manufacturers to deploy sensors throughout their facilities, providing them with real-time insights into the condition of their equipment.
- Increased Focus on Cybersecurity: As manufacturers become more reliant on connected devices and data analytics, they must also focus on cybersecurity to protect their systems and data from cyberattacks.
Predictive maintenance, powered by AI, is set to become an indispensable tool within the manufacturing industry. By embracing this technology, and proactively planning for changes, companies can position themselves for long-term efficiency and competitiveness. This data-driven approach promises to drive unprecedented levels of reliability and optimize manufacturing processes, solidifying the position of those businesses that embrace it.
Key Point | Brief Description |
---|---|
⚙️ Downtime Reduction | AI predicts failures, cutting downtime in US manufacturing by 15% by 2025. |
💰 Cost Savings | Proactive maintenance reduces unnecessary repairs and extends equipment life. |
📊 Data-Driven Decisions | AI analyzes sensor data for real-time equipment health insights. |
🤖 AI Technologies | Machine learning and deep learning power predictive maintenance systems. |
Frequently Asked Questions (FAQ)
▼
AI-powered predictive maintenance uses artificial intelligence to analyze equipment data and predict when maintenance is needed, reducing downtime and costs.
▼
AI algorithms analyze sensor data to identify potential equipment failures before they occur, allowing for proactive maintenance and preventing breakdowns.
▼
Predictive maintenance systems use data from sensors, historical maintenance records, equipment manuals, and real-time operational data to make predictions.
▼
The benefits include reduced downtime, lower maintenance costs, improved equipment reliability, increased productivity, and better resource allocation.
▼
Manufacturers can start by identifying critical equipment, gathering relevant data, choosing an AI platform, and integrating the solution with existing systems.
Conclusion
In conclusion, the adoption of AI-powered predictive maintenance presents a significant opportunity for US manufacturers to enhance efficiency, reduce downtime, and improve overall competitiveness. By embracing this innovative technology, manufacturers can proactively address potential equipment failures, optimize maintenance schedules, and pave the way for a more reliable and productive future.